Through design, testing, quality systems, and representation Ektor is committed and takes compliance and reliability seriously.
Dedication to
Compliance
Third-party testing
NATA and ILAC Mutual Recognition Arrangement (MRA)
Third-party testing is carried out by NATA certified test laboratories (Nation Association of Testing Australia) and other MRA certified Labs.
Australian testing laboratories, who have an approved scope and certification from NATA can produce test reports which have the NATA symbol. This stamp is critical to ensure the test is performed correctly and to the Australian Standard’s requirements.
Overseas testing laboratories, which also have an approved scope are accepted through the ILAC mutual recognition arrangement (MRA), where laboratories and reports carry certification from the respective certification agency within that country.
Examples of valid certified reports are detailed below:
- Australia – NATA
- China – CNAS
- Japan – JIS
- Germany – TUV
Additionally, when testing overseas it is critical that the lab tests the Australian deviations.
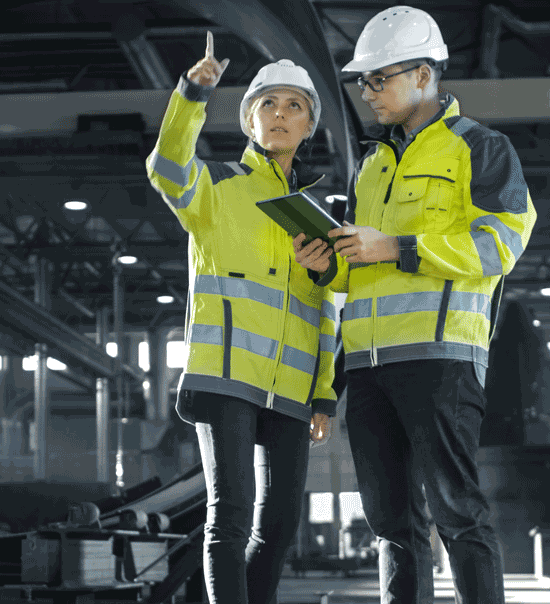
Key individuals
People
Knowledge, qualifications, and experience are extremely important to ensure products are designed and manufactured to the correct requirements. While our companies employ a large number of competent engineers, the following people are key to the success, quality, and compliance.
Allan has been in the lighting industry since leaving university and has a vast knowledge of emergency lighting and control standards.
Currently, Allan is a Standards Australia committee member of LG-007: Emergency Lighting In Buildings. Allan is also Australia’s representative to TC34-WG11 (control interface), is the author for IEC62386-305, IEC60386-306, and is the lead on IEC62386-201 Edition 2 (emergency lighting). Additionally, Allan participates in DiiA technical meetings and provides an expert opinion on control and emergency requirements.
Allan has vast experience in many lighting, emergency lighting, and device standards.
Reliability, certification, procedure
Quality system
A product that carries safety certification is not a guarantee that the product which is sold is safe. Changes in the supply chain, the in-house and on-line testing, and other variables all need to be managed to ensure safety. One product being safe does not mean all products are safe.
In our factories, our quality systems and procedures work to ensure safe, reliable, and repeatable outcomes in manufacturing.
Ektor’s emergency products are manufactured in Australian owned and operated factories which are certified and audited to ISO9001:2015. Some notable points are:
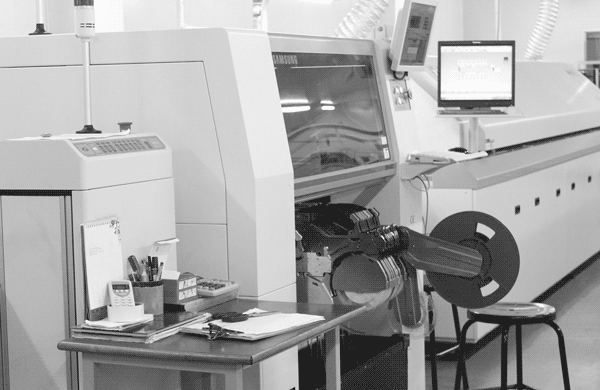
- Incoming goods inspectionsWhen receiving raw materials from suppliers, each item is checked against our documented requirements. Depending on the risk, some items can be batch tested while others may undergo a 100% inspection. Items like plastic are sent to batch testing to ensure they pass our Glow wire and flame tests, while stainless steel products would be tested for corrosion.
- On-line safety testingAll items undergo on-line safety testing to ensure the construction of the product is safe. A typical test like high-pot testing is applied to every manufactured product and is tested at a level higher than required.
- Function and reliability testingOur emergency products are put through on-line automated functional testing and on-rack reliability testing. Our reliability testing runs our products for up to 32 hours with increased environmental temperatures and maximum loads. Failure of a product during the reliability testing results in the immediate quarantine of the entire production batch and root-cause-analysis is performed to determine the failure case. Only when the quality department is satisfied will the products be allowed to continue.
- Batch testing and the Quality teamEvery production batch has a randomly selected number of items selected to undergo additional tests by our quality team. These tests are designed to ensure that the product performs and functions as defined.
- Traceability and recordsOur production lines are designed to take key metrics from production to help with efficiencies and traceability. Every PCBA carries a barcode which is used for traceability, these barcodes are scanned at different positions on the production line with the metric stored for future use. This allows us to understand the constitution of batches, the take-times for different processes, and the operator involved in each step among other things.
- The resultQuality products
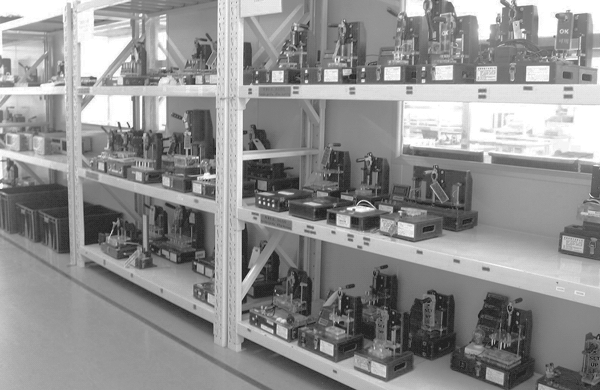
- Incoming goods inspectionsWhen receiving raw materials from suppliers, each item is checked against our documented requirements. Depending on the risk, some items can be batch tested while others may undergo a 100% inspection. Items like plastic are sent to batch testing to ensure they pass our Glow wire and flame tests, while stainless steel products would be tested for corrosion.
- On-line safety testingAll items undergo on-line safety testing to ensure the construction of the product is safe. A typical test like high-pot testing is applied to every manufactured product and is tested at a level higher than required.
- Function and reliability testingOur emergency products are put through on-line automated functional testing and on-rack reliability testing. Our reliability testing runs our products for up to 32 hours with increased environmental temperatures and maximum loads. Failure of a product during the reliability testing results in the immediate quarantine of the entire production batch and root-cause-analysis is performed to determine the failure case. Only when the quality department is satisfied will the products be allowed to continue.
- Batch testing and the Quality teamEvery production batch has a randomly selected number of items selected to undergo additional tests by our quality team. These tests are designed to ensure that the product performs and functions as defined.
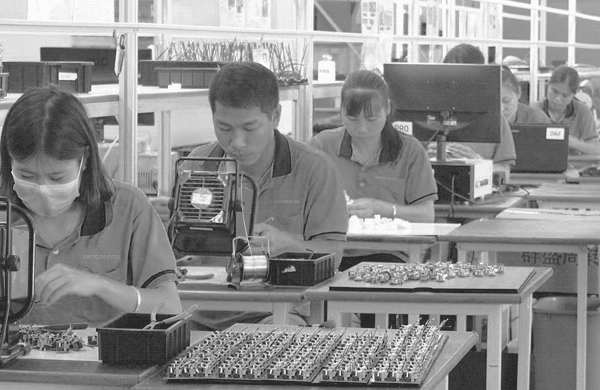
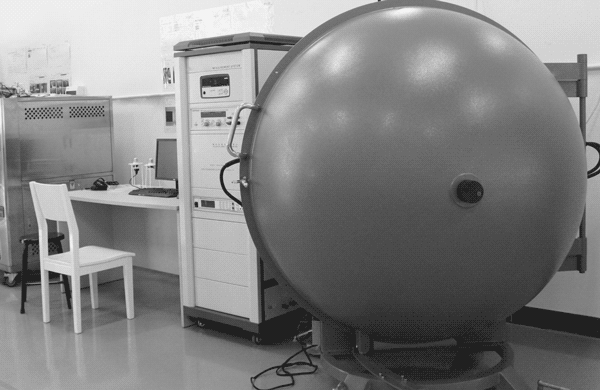
- Traceability and recordsOur production lines are designed to take key metrics from production to help with efficiencies and traceability. Every PCBA carries a barcode which is used for traceability, these barcodes are scanned at different positions on the production line with the metric stored for future use. This allows us to understand the constitution of batches, the take-times for different processes, and the operator involved in each step among other things.
- The resultQuality products
Certification
Declaration Of Compliance per AS2293.3 Appendix B
ACMA SDOCs
Australian Communications and Media Authority Supplier’s Declaration Of Conformity
Find your local distributor now